5 Dangerous Welding Defects: Know the Risks and How to Fix Them
- Luis Alejandro
- Nov 8, 2023
- 3 min read
Welcome to our latest blog post, where we delve into the world of welding to uncover the top 5 most dangerous welding defects. Welding is a critical skill used across various industries, from construction to manufacturing, but it's not without its challenges. These defects can compromise the structural integrity and safety of the final product, making it essential to understand their potential dangers and how to address them. In this article, we'll explore the dangers associated with each welding defect and provide practical solutions on how to rectify them. Let's dive in and ensure your welding projects meet the highest standards of safety and quality.
1. Porosity
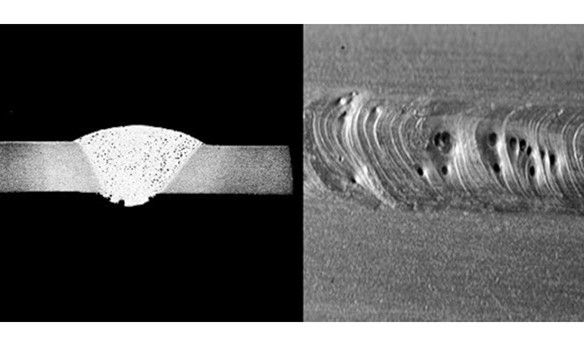
Why is it dangerous:
Porosity refers to the presence of small cavities or voids in the weld metal. These voids can weaken the structural integrity of the weld, leading to reduced strength and durability. Porosity can also compromise the weld's ability to withstand stress and pressure, making it highly dangerous in critical applications like pressure vessels or pipelines.
How to fix it: To prevent porosity, ensure that the base metal and welding equipment are clean and dry. Use proper shielding gas and follow the recommended gas flow rates. Maintain the correct arc length and travel speed during welding to minimize air entrapment. Properly bake and store electrodes to prevent moisture absorption.
2. Lack of Fusion
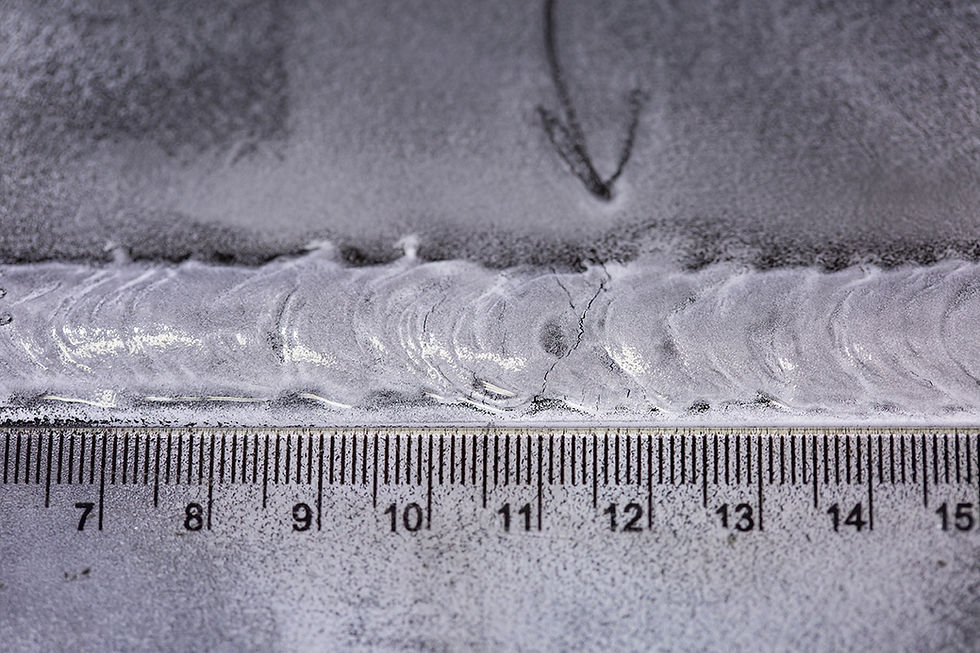
Why is it dangerous: Lack of fusion occurs when the weld metal fails to fuse completely with the base metal or previous weld pass. This defect can lead to incomplete joint penetration, creating a weak point in the structure. In applications where structural integrity is critical, such as in construction or aerospace, lack of fusion can result in catastrophic failures.
How to fix it: Ensure proper joint preparation, including beveling or grooving for full penetration. Maintain the correct welding parameters, including current, voltage, and travel speed. Verify the quality of the weld pool and the heat input to promote complete fusion.
3. Cracks

Why is it dangerous: Cracks in a weld can propagate through the material and lead to structural failure. There are different types of cracks, including hot cracks, cold cracks, and stress cracks, each with its own set of causes. Regardless of the type, all cracks are serious defects that compromise the weld's strength and safety.
How to fix it: Preventing cracks involves careful control of the heat input and proper preheating, especially when welding thick sections. Select appropriate welding techniques and electrodes to reduce the risk of cracking. Post-weld heat treatment may also be necessary for specific applications to relieve residual stresses.
4. Incomplete Penetration

Why is it dangerous: Incomplete penetration occurs when the weld metal doesn't fully penetrate the joint, leaving unfused gaps. This defect weakens the weld's structural integrity, especially in applications where full penetration is essential, such as pressure vessels or pipelines.
How to fix it: To avoid incomplete penetration, ensure proper joint preparation and fit-up. Adjust welding parameters to ensure adequate heat penetration and use welding techniques that facilitate full joint penetration. Adequate preheating and proper post-weld inspections can help mitigate this defect.
5. Excessive Spatter

Why is it dangerous: Excessive spatter is not inherently dangerous, but it can lead to safety hazards. Spatter consists of molten metal particles that can be ejected during welding. These particles can cause burns, damage equipment, and contaminate the work area.
How to fix it: To reduce spatter, maintain proper arc length and control your welding parameters, including current and voltage. Use appropriate shielding gas and ensure your equipment is in good condition. Regularly clean and maintain your welding gun and nozzle.
In summary, recognizing and addressing welding defects is crucial for safety and quality. Understanding issues like porosity, lack of fusion, cracks, incomplete penetration, and excessive spatter is key. By following best practices and precise techniques, you can mitigate these risks, ensuring strong, secure welds that meet high safety and quality standards.
Check out our other blog posts here https://www.southernarc.org/blog
About the author: Luis Alejandro is the owner and one of the instructors at Southern Arc Welding Services Ltd. Co.. He enjoys family, reading books on history, and writing to share his knowledge about the many situations welding can place us in.
Comments